Acetal vs. Delrin®: Their Differences
What is Acetal?
Acetal, also known as polyoxymethylene (POM), is an engineering thermoplastic known for its high strength, stiffness, and excellent dimensional stability. It is widely used in precision parts that require high stiffness, low friction, and excellent wear properties. Acetal is available in two basic types: homopolymer and copolymer. Homopolymer acetal provides slightly higher mechanical strength and rigidity, while copolymer acetal offers better chemical resistance and performs better in environments with high humidity.
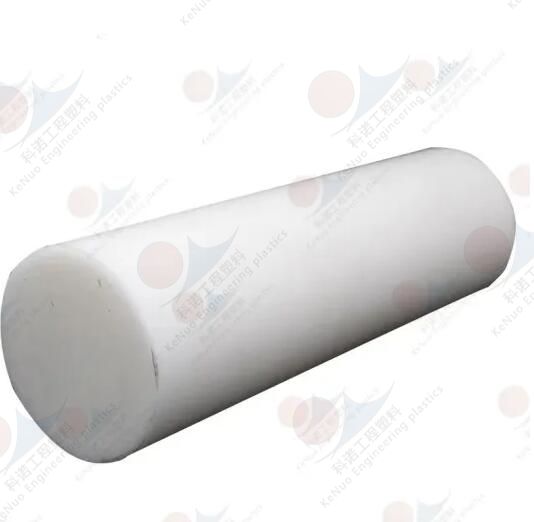
What are the Characteristics of Acetal?
Acetal's characteristics make it a highly versatile material. Key properties include:
- High Mechanical Strength and Rigidity: Acetal has high tensile strength and modulus of elasticity, making it suitable for mechanical applications.
- Low Friction and Excellent Wear Resistance: This makes acetal ideal for components like gears, bearings, and bushings.
- Dimensional Stability: Acetal maintains its shape and size over a wide range of temperatures and humidity levels.
- Good Fatigue Resistance: It can withstand repeated stress and strain, making it suitable for parts subjected to cyclic loading.
- Chemical Resistance: Acetal is resistant to many solvents, fuels, and other chemicals.
- Low Moisture Absorption: This ensures the material's properties remain stable in humid environments.
What are the Applications of Acetal?
Due to its unique properties, acetal is used in a variety of industries and applications, including:
- Automotive Industry: For parts like fuel system components, fasteners, and interior trim.
- Consumer Goods: In products like zippers, eyeglass frames, and handles.
- Industrial Applications: For gears, bearings, bushings, and other mechanical parts.
- Electronics: In connectors, insulators, and other components.
- Medical Devices: Used for manufacturing drug delivery devices and surgical instruments.
What is Delrin®?
Delrin® is a brand name for acetal homopolymer resin produced by DuPont. It is a type of acetal, but it offers distinct advantages due to its homopolymer composition. Delrin® is known for its superior mechanical properties and is often used in high-performance applications where strength, rigidity, and dimensional stability are critical.
What are the Characteristics of Delrin®?
Delrin® has several unique characteristics that set it apart from other acetal resins:
- Superior Mechanical Properties: Delrin® offers higher tensile strength, stiffness, and impact resistance compared to copolymer acetal.
- Excellent Fatigue and Creep Resistance: Delrin® can withstand repeated stress and maintain its shape under continuous loads.
- Low Friction and High Wear Resistance: Similar to other acetal resins, Delrin® provides excellent wear resistance and low friction.
- Good Chemical Resistance: It is resistant to various solvents, fuels, and chemicals.
- High Dimensional Stability: Delrin® maintains its dimensions over a wide temperature range and in humid environments.
- Enhanced Surface Finish: Delrin® offers a better surface finish, which is important for aesthetic and functional purposes in certain applications.
What are the Applications of Delrin®?
Delrin® is used in numerous high-performance applications across various industries, including:
- Automotive: In fuel systems, transmission components, and safety systems.
- Consumer Goods: For products requiring high strength and durability, such as gears, zippers, and clips.
- Industrial: In precision gears, bearings, and conveyor belts.
- Medical: For manufacturing reliable and durable medical devices and components.
- Electronics: In connectors, switches, and other electrical components.
What are the Differences Between Acetal and Delrin®?
While Delrin® is a type of acetal homopolymer, there are distinct differences between acetal copolymer and Delrin®:
- Mechanical Properties: Delrin® offers superior mechanical properties, including higher tensile strength, stiffness, and impact resistance compared to acetal copolymer.
- Fatigue and Creep Resistance: Delrin® has better fatigue and creep resistance, making it more suitable for applications involving repeated stress and long-term loading.
- Surface Finish: Delrin® typically provides a better surface finish, which can be crucial for certain applications requiring smooth surfaces.
- Chemical Resistance: While both materials offer good chemical resistance, acetal copolymer generally performs better in environments with high humidity and moisture.
- Cost: Delrin® can be more expensive than acetal copolymer due to its superior properties and brand premium.
Summary
In summary, both acetal and Delrin® are highly versatile engineering thermoplastics with a wide range of applications. Acetal copolymer is known for its good mechanical properties, chemical resistance, and dimensional stability, making it suitable for many standard applications. Delrin®, as an acetal homopolymer, offers enhanced mechanical strength, fatigue resistance, and surface finish, making it ideal for high-performance and demanding applications. Understanding the specific requirements of your application will help determine whether acetal copolymer or Delrin® is the better choice.
Copyright and Trademark Statement
Delrin® is a registered trademark of DuPont. The information provided in this article is for educational and informational purposes only and does not constitute an endorsement or recommendation of any specific product or brand. All trademarks and registered trademarks are the property of their respective owners.